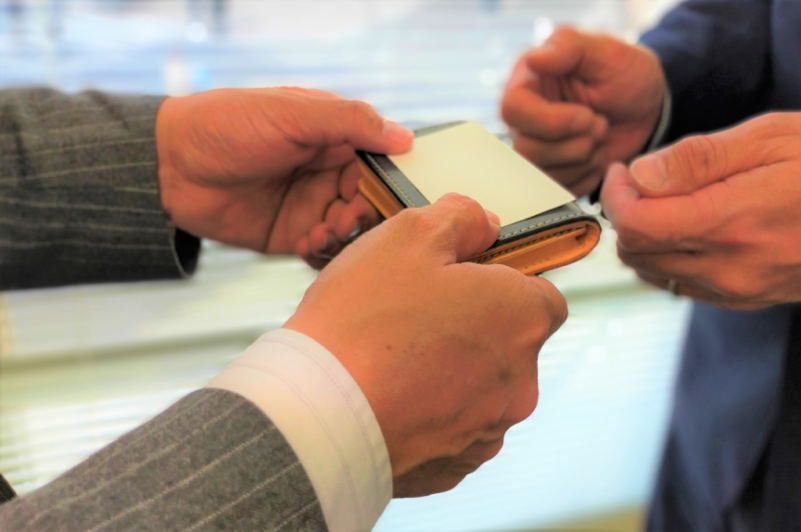
As a sales representative
I belong to the sales department. The sales staff not only serve as a point of contact with customers, but also play a role in connecting them with various departments of our company.
The project that I am introducing here is one of our largest projects, which took two and a half years from the time we receive an inquiry from a customer to the completion of a series of processes, including submission of the quotation, conclusion of the contract, the design and manufacture of the equipment, and delivery coordination.
As sales department, it was very difficult to reach a point where we could receive an order of this large-scale project since there were other companies in the same industry. I think if we hadn’t had a strong continuous relationship of trust between the customer and us, we wouldn’t have secured the order. I suppose that the customer checked all aspects of our capabilities such as planning, engineering, manufacturing, adjustment, and response. There may have been some twists and turns until we received the order, but I believe that having built a trust relationship with the customer over 20 years enabled us to get the order.
By the end of the project, the number of business cards I had received from customers and other involved was enormous. Working on the project for two and a half years, I had a valuable experience of feeling like a member of the community to complete the same project, regardless of the position of a customer or manufacturer.
It was a very emotional project for me, since I found it extremely rewarding and felt a sense of accomplishment that I had never experienced before.
Department Manager
Sales Department